Experimental EV battery charges in 10 minutes in sub-zero temperatures
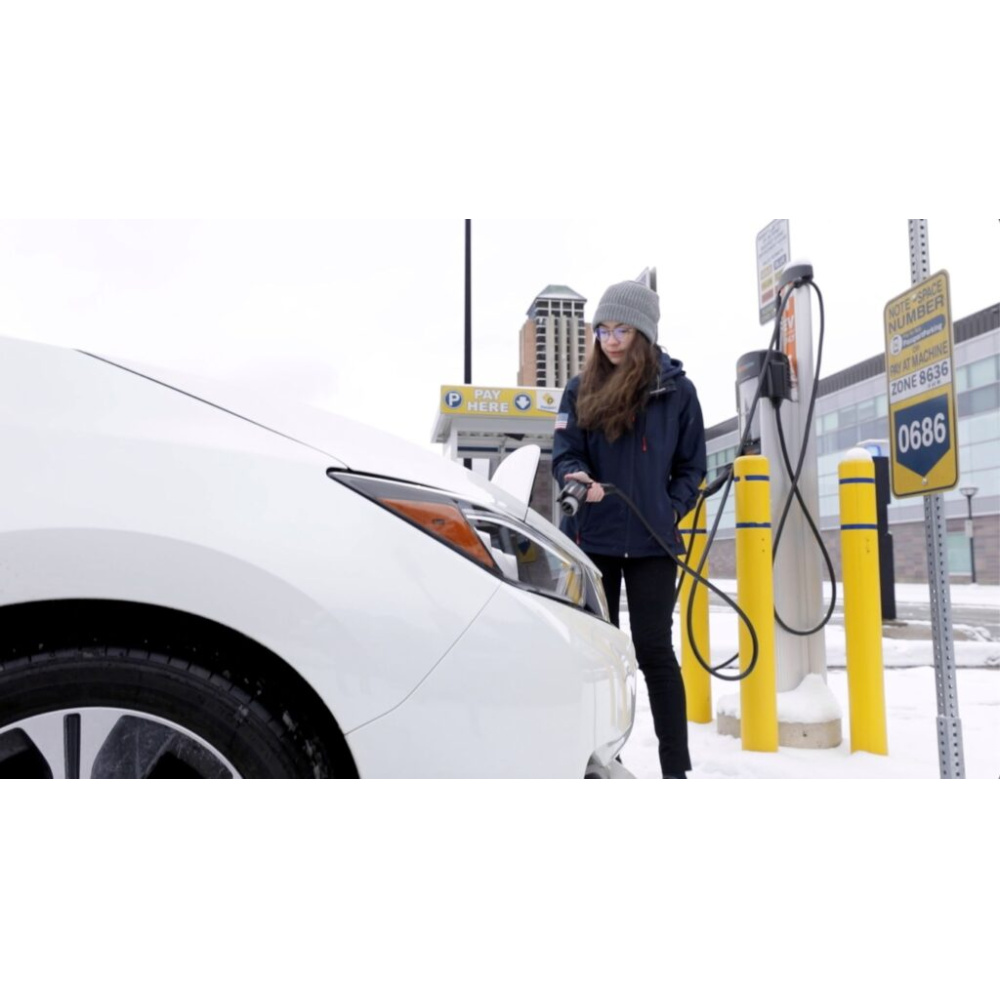
Researchers from the University of Michigan have developed a lithium-ion battery (LIB) for electric vehicles (EVs), with only 10 minutes of charge to full in temperatures as low as -10 C.
The new technology is licensed and is to be commercialized by Michigan’s Arbor Battery Innovations.
“This is fast charging without compromise,” said Dr. Andrew Davis, CEO of Arbor. “We’re not asking battery makers to change chemistries or reconfigure production. Arbor fits into the battery factories of today – and delivers the performance tomorrow demands.”
Current EV batteries store and release power through the movement of lithium ions between electrodes via a liquid electrolyte; however, in cold temperatures, this movement is slowed, affecting the charge. To solve this, automakers have increased the thickness of the electrodes they use in battery cells. However, that came with a drawback, resulting in a slower charging time.
To solve that issue, previous literature has suggested the creation of highly ordered laser-patterned electrodes (HOLEs) consisting of arrays of vertical channels. Those can serve as linear pathways for rapid ionic transport into the bulk electrode, significantly speeding up room temperature charging. However, it has failed doing so under cold environment, due to Li plating, an unwanted deposition of metallic lithium on the anode surface.
“Li plating becomes an increasingly important source of capacity loss and cell degradation,” said the research team. “Thermodynamically, Li plating can occur when the potential of the negative electrode drops below 0 V vs. Li/Li+, although a kinetic barrier for Li nucleation also exists. Furthermore, the spatial inhomogeneity in local current density, both through the electrode thickness and within the x-y plane, plays an important role in the onset of Li plating.”
Neil Dasgupta, a U-M associate professor of mechanical engineering and materials science and engineering and the corresponding author of the study, compares this behavior to that of butter. “You can get a knife through it whether it’s warm or cold, but it’s a lot harder when it’s cold,” he said. “If you try to fast charge through that layer, lithium metal will build up on the anode like a traffic jam.”
To prevent the surface layer from forming, the researchers coated the battery with a 20-nanometer-thick glassy material. The coating, a single-ion conducting glassy solid electrolyte (Li₃BO₃-Li₂CO₃) known as LBCO, was applied to industrially relevant pouch cells (3.2 mAh/cm²) using atomic layer deposition (ALD). The team compared four battery types: control, HOLE alone, LBCO alone, and an LBCO-HOLE hybrid.
“Electrodes that incorporated the synergistic LBCO-HOLE treatment condition achieved >92% and >97% capacity retention over 100 cycles of 4C (15 minutes) and 6C (10 minutes) charge rates, respectively, at a temperature of -10 C,” said the scientists. “In contrast, the capacity of uncoated control and HOLE anodes dropped sharply below 50% after the initial fast-charging cycles at -10 C as a result of severe Li plating.”
The analysis found that uncoated graphite cells retained less than 20% of their accessible capacity (state of charge, or SoC swing) after 20 cycles. In contrast, LBCO-HOLE cells maintained around 70% SoC after 15 minutes at a 4C rate and about 55% after 10 minutes at a 6C rate. The researchers concluded that this improved rate capability by more than 400% at 4C and over 500% at 6C.
It presented the novel battery in “Enabling 6C fast charging of Li-ion batteries at sub-zero temperatures via interface engineering and 3D architectures,” published in Joule.